Wing structures and Additive Manufacturing (aka Trip to England pt 2)
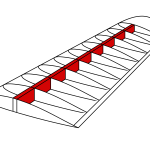
Here comes another part of the story of our trip to and through England. Our first visit was Western Approach, the GKN site in the outskirts of Bristol. There we got to see their production of wing spars in spacious buildings and new machines. Spars are load bearing structures of wings seen in the figure on the right. Anyway, the production was, at the time of visit, focused on Airbus’s new A350 program and the military transport aircraft A400M Atlas (turboprop).
Producing the spars begins with a technique called Advanced Fiber Placement (AFP), in which tows of epoxy impregnated carbon fibers are robotically placed onto a mandrel. Layer upon layer of strategically placed material, reinforces the structure where it’s needed and minimizes the weight of the finished product. To get rid of porosities and promote complete bonding between fibers and epoxy, a pressurized oven (an autoclave) is used for the hardening process. Defects are checked for before painting seals the surface and the deal.
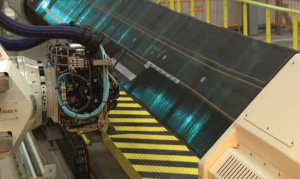
The composite spar structures are machined to dimensions and drilled for the installation of connecting parts, such as landing gear brackets and wing flap mounts. The assembly here avoids static fixtures which traditionally are used for such large parts. Instead, movable jigs skid along the building floor from one process step to the next and saves requirements for machine duplicates etc.
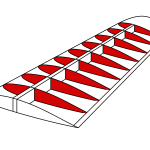
Similarly to Western Approach, another subject of visit and site in Bristol (or Filton) also works with the production and assembly of wing structures. The Filton plant manufactures the wing ribs, the parts perpendicular to the spars which define the shape of the wing (see figure). The ribs are CNC milled from thick base material slabs down to shin sheets with incorporated stiffeners to increase rigidity and reduce weight.
The costly yet necessary waste of material and generous time spent in machines has awakened the attention for a manufacturing technique on the rise. 3D-printing or Additive Manufacturing, as it’s referred to less populisticly, offers the possibility to form the stiffeners right onto the sheet product, thus potentially could save a lot of material and machining compared to conventional fabrication. Investments in the technology have resulted in the Centre of Excellence of the so called powder bed process at the site in Filton. Here, fabricated models show how changes in the design enables optimized structures for existing components, but the full potential of the technique requires redesign of interdependent structures, bluntly the whole aircraft.
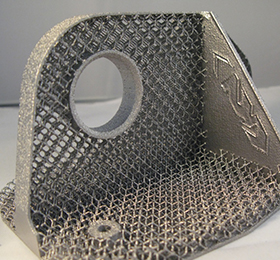
Our last visit of our trip was the Imperial College where the Department of Aeronautics conducts research on Additive Manufacturing. We met with Dr Francesco Montomoli, Dr Rob Hewson and some of their postgraduates, who presented ongoing studies in the field. They work on design and manufacturing of aerospace products through Additive Manufacturing, but also development of programs that are able to disregard design restrictions, set by earlier means of production. With new possibilities, the solution to future problems (design of aircrafts) may come from AM.
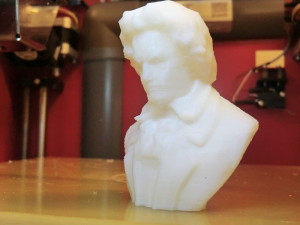