Study visits in California
Besides working, me and Linn have had the opportunities to go on study visits to GKN SItes and suppliers around California. Here follows a short
We’ve been to GKN in El Cajon, together with high school students and teachers from GKN in Trollhättan. The site is also part of the Engine Systems division and manufacture products similar to those made in Sweden. This includes cold and hot structures, static and rotating parts, from turbine blades to giant fan cases. One of their processes, called chemical milling, is rather unique and is used to manufacture ribs, reinforcements and flanges in sheets and complex designs. The process’s high removal rate through etching is the result of baths with strong and hot acid, which have required rigorous controls to maintain permission to use it.
[A picture from our visit to Camarillo will be added soon :O ]I and Linn have also been to Carlton Forge Works outside Los Angeles. As suggested by the name their main business is forging, large and difficult forgings like turbine cases, fan cases (those later machined in El Cajon), spools and flanges for their biggest customer, GKN Aerospace. The forgings are huge and so are hammers, presses and rollers.
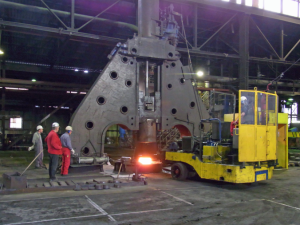
TIMET refines and manufactures titanium alloy products, primarily to the aerospace industry. Located in Henderson, close to Las Vegas, is their plant for extracting titanium from rutile ore, which we got to visit last month. Through a series of stages the pure titanium is separated from titanium oxide, reacted to chlorine, distilled and combined with magnesium. The product is a large, porous cylinder (titanium sponge) and has thus far required a lot of energy. Luckily, the plants location in the middle of the desert is also close to the Colorado River and the electricity producing Hoover Dam.
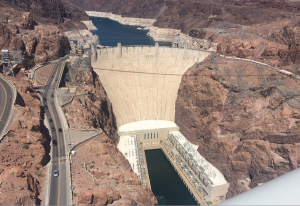
Next week, we’ll be going to the small GKN factory in Camarillo, west of Los Angeles, where they form sheet metal exclusively using metal spinning. The sheet metal is clamped onto a mandrel and, while rotating, is pressed with a roller tool against a die. The formed components (lip skins) sit in front of the fan and protect the inlet from impacts, abrasion and heat from the anti-ice air supply.
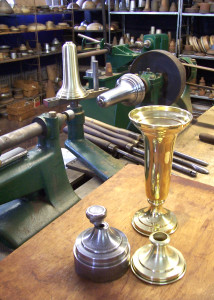
I need to go and prepare for the upcoming celebration of the Independence Day. Have a nice weekend!
Mikael