Workshop practice
Hello everyone!
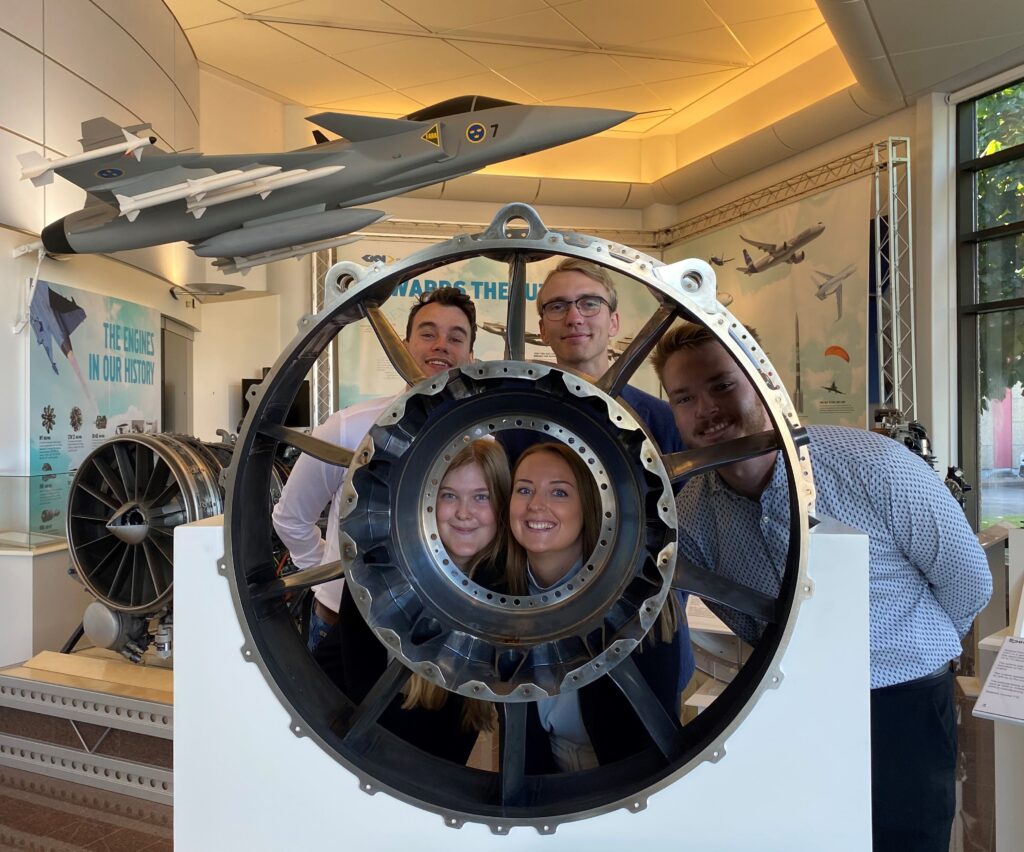
For the past two weeks, we have had workshop practice. We have all observed individual parts and their journey through the flow of operations here at GKN Aerospace in Trollhättan. Today was the final day of the workshop practice and we presented our learnings from the weeks to each other. Below is a brief description of our experience.
Elias: I spent my introductory workshop period at the Rotatives department in the X-workshop, where I followed the production sequence of an LPC (Low Pressure Compressor). The LPC is one of the first steps of a conventional jet engine, with the purpose of initializing the compression of air before the following engine parts. Rotating parts of a jet engine usually have strict requirements when it comes to tolerances, so through this workshop period, I had the opportunity to see the methods that GKN Aerospace use to accomplish these requirements. The manufacturing process included conventional machining, such as milling and lathing, but also included more advanced metallurgical control and measuring methods. In conclusion, it was very insightful to have the opportunity to observe part of GKN’s operations and see what some of the challenges are in a manufacturing process.
Emelie: During my time in the workshop, I had the opportunity to follow a product called 30k TEC. The name does not really say much initially, but 30k is a name used for motors that generate a thrust of around 30 000 lbf, or approximately 135 kN, and TEC stands for Turbine Exhaust Case, which means that it is located after the turbine in the engine. During my time in the workshop I saw the product transform from just a box of components to a finished product, which has been a lot of fun! Before this, I had never set foot in a workshop, but thanks to this experience I know a lot more about what it is like to work in a workshop. Every day I got to follow a new process, and I have learned about everything from welding and X-ray to turning and milling.
Alexander: The last two weeks I’ve spent at Structures in the C-shop. I had the opportunity to follow XWB, a large static part that resides in the Trent XWB (Rolls-Royce) engine, powering the A350-900. The part is welded together from smaller sections and if that was not cool enough, LMD (Laser Metal Deposition) is utilized to build up the profile. It has been a great opportunity to meet co-workers and gain a better understanding about the products produced in Trollhättan.
Merim: During my workshop practice I’ve been assigned to the RM12 engine, which powers Sweden’s own Gripen fighter jet. I’ve previously never seen an RM12 engine, in fact I’ve never seen a jet engine except for pictures, and to see one in reality was a real experience! I have got the privilege to see all the individual components that are inside, which all contribute to the successful operation of the engine. I am glad for getting the opportunity of seeing an RM12 engine, it has been immensely fun and I am very grateful for everything I have learned by the best within the field of RM12.
Moa: During my workshop practice I have been with the department Spools and Special Processes and followed the part LM2500. LM2500 is a part that is not used in aviation, as LM stands for Land & Marine. The part is a spool covering step 3-9 in a gas turbine compressor and is a rotating part with strict tolerances. It has been very interesting to follow the production flow of the part as it moves diligently through the plant and I have learned a lot about different processes used here in Trollhättan.
In conclusion, it has been a very rewarding time, and we are all extremely grateful to everyon that has taken the time to guide us and help us understand what they are working with! We are now looking forward starting our first rotation.