Workshop internship
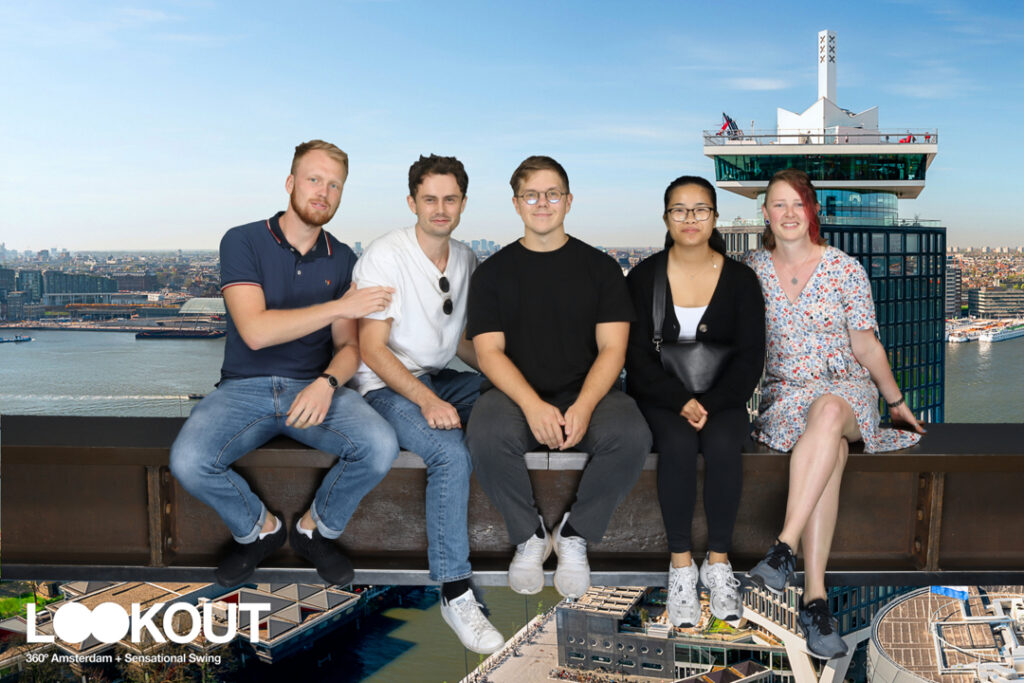
Hello again!
It’s been a while since we last posted and as we mentioned in the previous post, we were just about to finish one of the two weeks of the internships in the work shops. The point of the internships is for us to follow the journey of one detail through the different production streams here at GKN Aerospace Trollhättan. The internships ended last week but yesterday we held some presentations and tours for each other so show what we have seen and learnt these past weeks. And if you are curious about our experience, keep on reading!
Linus: Time flies when you’re having fun! Two weeks of internship at Civil Aftermarket a new organization within GKN dedicated to MRO (maintenance, repair and operations) on civil engine parts. My first week was spent in A-shop to look at repairs and upgrades of parts to the PW1000g engine. The second and last week was spent on LM (Land and Marine) where I got to disassemble a DR990 IGT (Industrial Gas Turbine) for further repair operations. Thanks to all who made these two fun weeks happen!
Rasmus: I spent my workshop internship at Spool and special processes in the-C workshop where I followed two products, a 2-5C and a 3-9C. A 2-5C sits in one of the very first stages in a jet engine, it has the task of compressing air before the next stages in the engine. A 3-9C sits a few stages further down in the jet engine, it also has the task of compressing air, but at a much higher frequency. Spools are rotating parts in a jet engine which come with very strict tolerance requirements, I as an intern therefore had the opportunity to see how GKN Aerospace ensures that these strict requirements are met. The manufacturing process included CNC machining with both lathe and milling but also a number of special processes that ensure that the product is of good quality. The special processes were very interesting to see as I didn’t know they were used in the aerospace industry, some of the special processes I got to see were ultrasonic, blue etching, penetrant and thermal spraying. In summary, it was very rewarding to see part of GKN’s operations and the challenges that exist when manufacturing parts for aircraft engines.
An Na: I spent my two weeks in the X workshop where I got to follow the work stream of some parts for a detail called 30k TEC. The name of the detail can be divided into two parts where 30k represents motors that generates thrust of 30 000 lbf. TEC is a just acronym for Turbine exhaust case which means that the detail is positioned after the turbine in the motor. Since I’m not very familiar with the workshop enivronment, I think the internship has been very rwewarding since I got to see a lot of how things works when the products are manufactured. Also, I got to meet many knowledgable and funny people during these weeks which was very nice!
Arvid: One of the most memorable experiences from my time in the workshop was to try out welding for my first time. After some instructions from “Tabasco”, I managed to get under the welding helmet to weld two Inconel 718 plates together. It didn’t go well, as the pictures below shows, but the plates are at least welded together. Some things I would need to improve in order to pass the welding test are steadier hands when adding material and to keep the beam closer to the material. Hopefully not my last time!
Rebecka: I followed the production cycle for the Ariane nozzle, from the sheets of metal arriving until the finished product was shipped to the customer. I had never been in a workshop before and of course the first thing I noticed were the huge machines, but also the community amongst the employees. Many of them have worked at GKN for several years and they were like a big family, which they quickly welcomed me into.
I had two fun weeks where I learnt a lot, it was very interesting to get familiar with every step of the process that the nozzle goes through and of course, to get to see a fully finished nozzle! It was a perfect start for me since my first rotation is at Nozzle and I had use of my knowledge from the workshop from the first day.
To sum up, we all had a great time in the work shops and we have all learnt plenty. So we want to give the people who shared their knowledge with us a big shoutout!
Now we have lots of fun stuff is coming up, so stay tuned for that!