Visit to Filton
Our third visit where as previous mentioned to the GKN Aerospace Aesrostructures site in Filton, Bristol. But before I start to discuss the visit I just want to take the time and thank everyone that we met during the whole week. Everyone took really good care of us and I felt truly welcome wherever we went.
So about the actual visit, in Filton GKN are sharing an enormous area (74.000 m2 floor space) together with mainly Airbus. Much like us in Trollhättan, Filton is also fairly new to the company, acquisitioned in 2010 from Airbus. Because of this, the site naturally works very close with Airbus and was as late as 2014 announced ‘best performing supplier’.
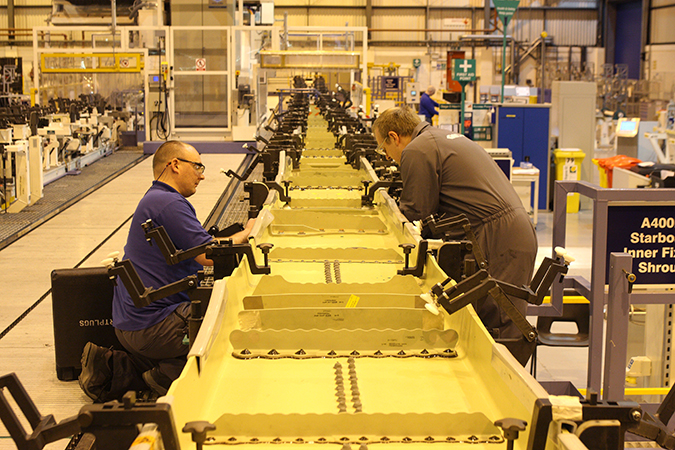
Our host and coordinator for the day was Tracy and she had a truly rigorous schedule planed for us. After a shorter introduction we started with a shop floor tour through the assembly of the leading edge to the A330/A340 wings and A400M spars. This experience was in many ways differencing itself from ours by the amount of manual work. The tour followed the different assembly zones until we ended up with the final assembly. Later in the day we also had the chance to see the A380 trailing edge assembly. This assembly line was newer and had more automation implemented and the dimensions where truly astonishing. Maybe not so strange since the A380 has a wingspan of impressive 80 meters.
Besides the work shop tours we also got to see the work and development made in the area of additive manufacturing as well as a presentation of the Engineering capabilities within aerostructures by Max Brown, head of Engineering operations.
The difference using additive manufacturing from more traditional manufacturing methods is that instead of removing material from a larger structure, material is added layer by layer until the desired 3D structure is achieved. A lot of research and developing are made in the aerospace industry within this area. As the technology matures and the cost decreases we probably are going to see more and more 3D printed parts. However a lot of challenges still exist and certifying the methods for the aerospace industry will probably take some time. Below I have attached a short film regarding additive manufacturing that I personally thought was interesting.
Finally I just want to thank Filton and everyone taking care us during our visit and a special thanks to Tracy for planning our visit.