“I’ve never known an industry that can get into people’s blood the way aviation does.” – Robert Six, founder of Continental Airlines.
This past week, myself and the other Trainees here in Sweden traveled to Paris to learn more about this infectious industry as well as meet some of our customers who rely on GKN to help them create today’s most powerful jet (and rocket) engines.
We visited the Safran aerospace museum where we were given an in-depth private tour to understand some of the forces that shaped the aerospace industry from its inception into what it is today. From some of the simplest propeller engines to todays most advanced jet engines we learned about the historical context that surrounded certain advances in flight, and the influence of that historical context on aerospace development and vice versa, such as the jet engines role in the outcome of World War 2.
At the Paris Airshow we saw some incredible flying displays from some of the most elite aircrafts in today’s market. Among some of the demonstrations include:
- Pipistrel MOD 167 Alpha Electro
- Dassault Falcon 8X
- Turkish Aerospace Industries ATAK 129 Helicopter
- Airbus A330neo
- Airbus A350-1000
- Boeing 787 Dreamliner
- Pakistan Aeronautical Complex Kamra-JF-17 Thunder
- And last but not least… The Dassault RAFALE
These demonstrations cemented our love for what we do. What this industry is capable of is nothing short of incredible and I’m proud to be a part of these incredible feats of engineering and science. Further, this new knowledge of what we’ve achieved in the past 100 years, and where we are today has inspired me to look forward to what we can be 100 years from now.
At the forefront of Aerospace technology is Ariane Group, who graced us with a tour of their site in Vernon where they showed us the assembly lines for the Ariane 5 & 6 engines as well as a showcase of some of their other engines such as HM7B, Vinci, Vulcan 1, and Viking. They also showed us the test sites for these engines, but unfortunately no tests were scheduled for the day of our tour. Finally, we talked to them about the Ariane 6 development process, examples, and the increase in additive manufacturing for many of the sub-assemblies on this engine (a subject very relevant to what I am working on now).
Lastly, we visited two startups related to Industry 4.0: Scortex and Ubudu. The team at Scortex is working on harnessing the power of AI and machine learning to help with visual inspection. They gave us a thorough explanation of how they are able to use machine learning to spot defects in a variety of parts in several different industries. Ubudu is a slightly older startup that has been developing solutions for indoor location tracking (again for a variety of different industries). For us, this technology could be used to track parts and batches through our factories, create spaghetti diagrams, and even automate forklifts and inventory control systems. These presentations gave us valuable insight as to what the fourth industrial revolution can mean to GKN factories in the future. Using AI to correlate measurable machine parameters to dimensional inspection results, suggest corrective action, schedule and optimize production throughout the factory and machine maintenance, and level load operations are just some of the potential applications for this technology and I cannot wait to see that transformation take place.
For me, working for GKN means much more than making parts for aircraft engines. It’s about the role that those parts play in connecting people around the world in a safe, sustainable, and efficient manner, as well as the impact that we can have on humanity by making travel more accessible to people from all walks of life. The more people travel, the more we learn and grow as a species, and in that regard, aviation is in my blood.
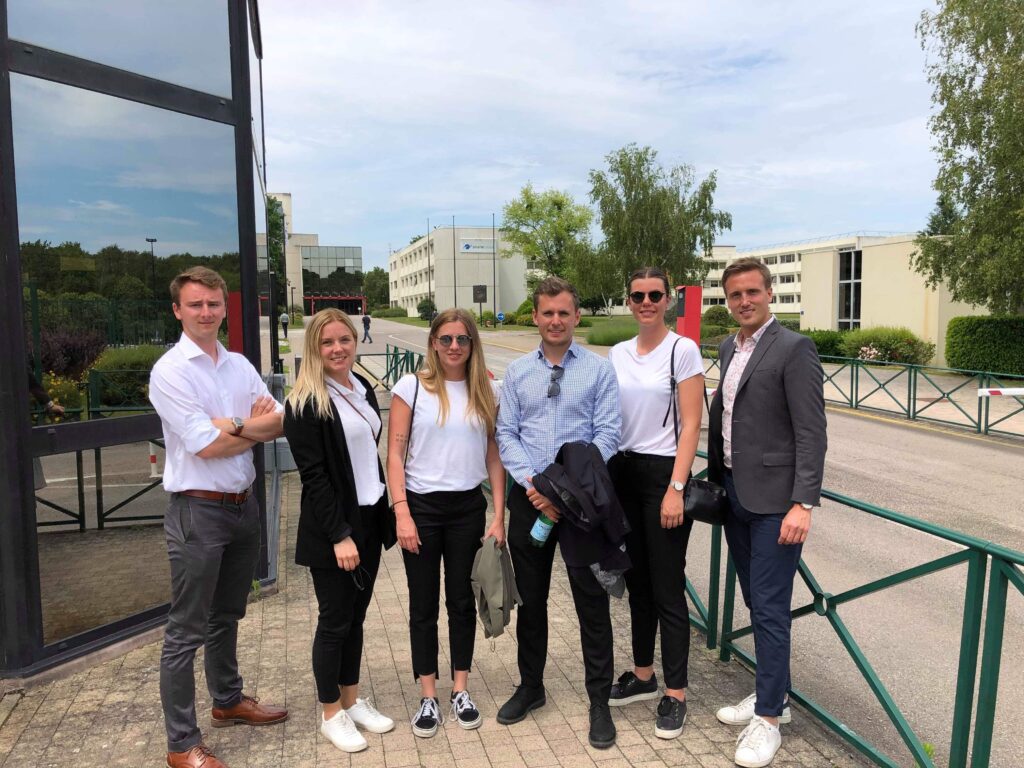