Verkstadspraktik på LPT
Även jag, Anders, har nu tillbringat lite drygt en vecka i verkstaden. Jag har blivit utstationerad på avdelningen där man tillverkar LPT cases, det vill säga det hölje som innesluter den lågtrycksturbin som sitter i motorns bakre ände. Eftersom denna del måste kunna utstå extrem hetta används en rad mycket hårda och, för mig, exotiska material. De LPT cases som GKN tillverkar i Trollhättan är av en mängd olika storlekar, där de mindre bland annat sitter i motorer till Airbus A320 och de största i Airbus A380. En del är även tänkta att monteras i mer stationära gasturbiner för elproduktion på land och i fartyg till sjöss. Tillverkningen här består till största delen av klassisk skärande bearbetning, såsom svarvning, fräsning och borrning, men även montering och några avtvättningar ska hinnas med innan detaljerna i skinande skick når den noggranna inspektören i slutkontrollen (se bild).
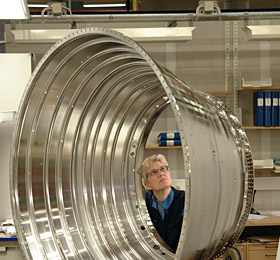
För mig med mer begränsad kunskap i materiallära och bearbetningsmetoder har den största aha-upplevelsen istället kommit av att se hur flödet av produkter fungerar i en fabrik med långa bearbetningscykler och hårda toleranskrav. I jämförelse med bilindustrin, där man utan större tvekan kan rulla ut nytillverkade bilar med 60 sekunders mellanrum, kändes flödet i av LPT cases till en början nästan stillastående. Det jag insett under praktiken är att det inom flygindustrin inte finns något behov av att trycka ut tusentals produkter i veckan och att det inte finns några större vinster i att jaga sekunder i enskilda tillverkningsmoment, när varje bearbetningsoperation kan ta flera dagar att genomföra. När man förstått detta upplevs flödet av LPT cases plötsligt mycket mer välordnat.
Vad lågtrycksturbinen för övrigt fyller för funktion i jetmotorn är för mig ännu en gåta och kan komma att förbli det tills vi har gått den obligatoriska kursen i flygmotorlära. Jag hoppas kunna återkomma med en förklaring då!